▶️ Watch Now: How Do Electric Motors Turn Electricity into Motion? Discover the Hidden Power Behind the Spin!
This video gives you a fast and clear explanation of how electric motors convert electric current into mechanical movement. Starting with the interaction between magnetic fields and current, we’ll break down the roles of the rotor, stator, brushes, and brushless designs. You’ll also see a simple hands-on experiment that brings the motor’s magic to life.
Introduction: The Invisible Force Behind Our Everyday Life— Electric Motor
You may not have noticed it, but electric motors have quietly become the hidden driving force of modern life.
When you turn on a fan, it spins. When you use a washing machine, it spins. When you ride an electric scooter—it spins again. From printers in the office, to vacuum cleaners at home, to infusion pumps in hospitals and conveyor belts in factories, motors are everywhere, powering the world with every turn.
But here’s the real question: How does electricity become motion?
Why should we understand how motors work?
And what does this have to do with electromagnetic induction?
This article takes you step by step from the core principles and internal structure of electric motors to their different types and real-world applications—so you can finally understand the magic behind “electricity in motion.”
Chapter 1|What Is an Electric Motor?
An electric motor is a device that converts electrical energy into mechanical energy—in other words, it turns electric current into rotational force.
Its operating principle is the reverse of a generator:
Device | Function | Energy Direction |
---|---|---|
Generator | Converts mechanical energy to electricity (e.g. hydropower) | Motion → Electricity |
Motor | Converts electricity into mechanical energy (e.g. spinning fan blades) | Electricity → Motion |
While this energy conversion may seem simple, it’s grounded in the deeper laws of electromagnetism.
Common Types of Electric Motor :
- DC Motor (Direct Current)
Uses a commutator to produce unidirectional torque. Simple to control and fast to start. - AC Induction Motor
Generates torque via magnetic field induction. Highly durable and commonly used in industrial settings. - BLDC Motor (Brushless DC)
Modern, efficient, and compact. Ideal for drones, tools, and precision electronics.
Chapter 2|Basic Components of an Electric Motor
Though the design varies by type, most motors share these essential components:
🔹 Rotor
The “heart” of the motor—this rotating part usually has a coil or conductor loop. When current flows through it inside a magnetic field, torque is generated, causing it to spin.
🔹 Stator
The stationary part of the motor that provides a stable magnetic field (via permanent magnets or electromagnets). In induction motors, the stator produces a rotating magnetic field.
🔹 Brushes and Commutator (DC motors only)
Brushes transfer current to the rotor via the commutator, which reverses the current direction every half turn, ensuring continuous rotation in one direction.
🔹 Bearings, Housing, and Cooling System
- Bearings: Allow the rotor to spin smoothly
- Housing: Provides structure and insulation
- Cooling: Prevents overheating during prolonged or high-speed operation
Chapter 3|How Does Electricity Become Motion?
📌 Key Principle: Lorentz Force
When an electric current passes through a conductor inside a magnetic field, it experiences a force—this is defined by the Lorentz Force Law:
F = BIL
F = Force, B = Magnetic Field Strength (Tesla), I = Current (Amps), L = Length of the conductor (Meters)
This force causes the conductor to move, producing rotational motion.
🧲 A Simple Example: One Wire, One Push
Place a straight wire between two magnets and run current through it—
You’ll see the wire jump sideways. That’s the most basic form of electromagnetic force in action.
🔁 Real-World Implementation: The Coiled Rotor
To keep motion continuous, the conductor is wound into a multi-turn coil, fixed to a rotor. As it rotates within a magnetic field, the loop constantly experiences Lorentz force, driving stable rotation.
In AC motors, the alternating current naturally produces a rotating magnetic field, sustaining motion.
In DC motors, the commutator switches current direction every half turn, keeping torque in the same direction.
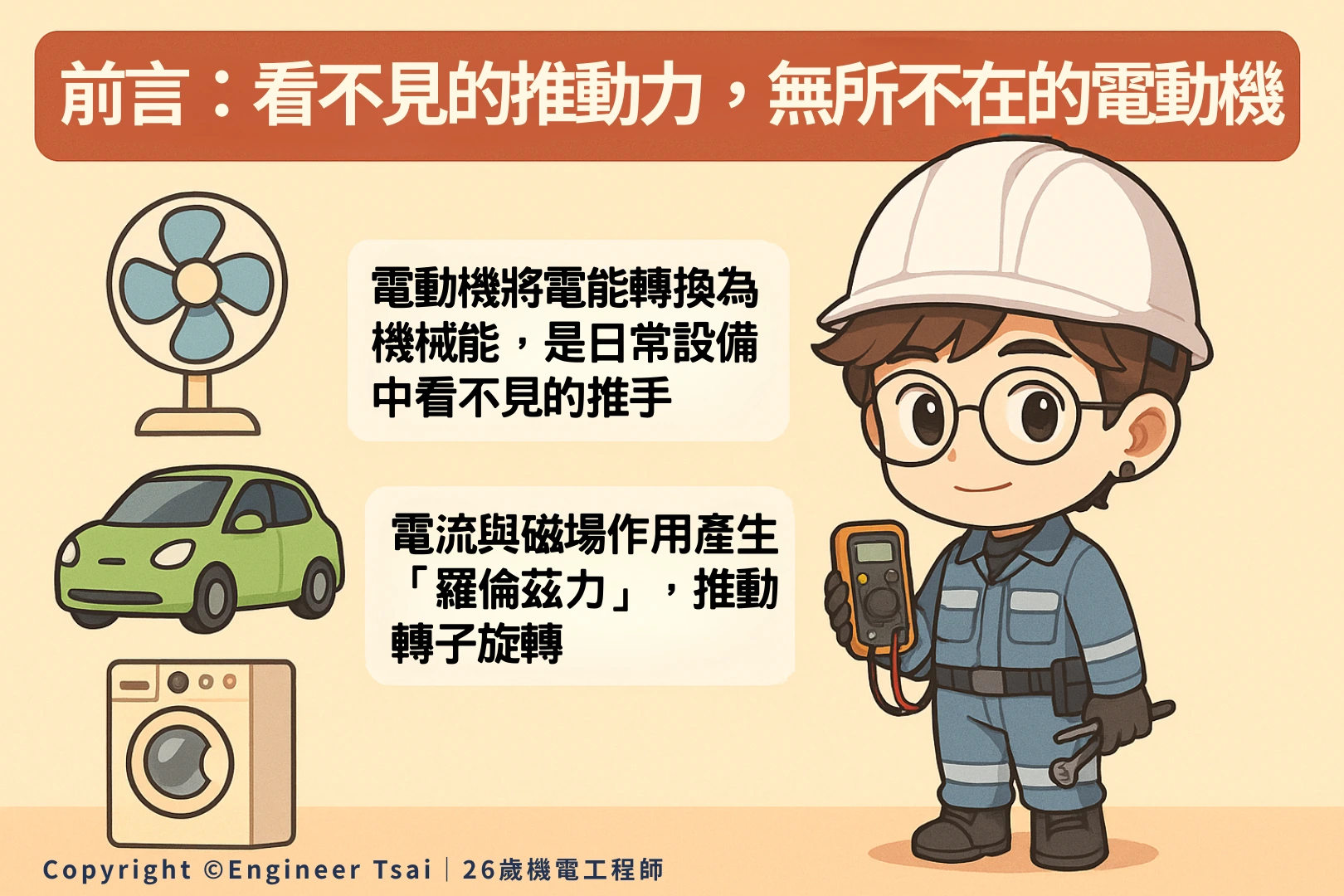
Chapter 4|Comparing Different Types of Electric Motor
All electric motors convert electrical energy into mechanical energy—but their structures and driving methods vary significantly. Below are the three most common types and how each one works:
✅ DC Motor (Direct Current Motor)
DC motors are among the oldest and most widely understood types, often used in educational and simple control systems.
- Key Components: Rotor, stator, carbon brushes, and commutator
- How It Works: The commutator and brushes alternate the current direction, keeping the torque consistent to maintain continuous rotation
- Advantages: Easy to control, high starting torque, good for variable speed applications
- Common Uses: RC cars, small fans, handheld tools, educational kits
✅ AC Induction Motor
This type is heavily used in industrial applications due to its rugged design and reliability.
- Key Components: Stator windings and squirrel-cage (or wound) rotor
- How It Works: Alternating current creates a rotating magnetic field, which induces current in the rotor. The interaction produces torque
- Advantages: Durable, low maintenance, long lifespan
- Common Uses: Air conditioners, water pumps, conveyor systems, elevator motors
- Subtypes:
- Single-phase motors: Ideal for small household devices
- Three-phase motors: Standard in high-power industrial equipment
✅ BLDC Motor (Brushless DC Motor)
BLDC motors are a fast-growing, modern motor type, well-suited for compact and high-efficiency systems.
- Key Components: Permanent magnet rotor, stator windings, electronic controller, Hall-effect sensors
- How It Works: Sensors detect rotor position, allowing the controller to precisely switch current flow and maintain rotation
- Advantages: No brushes, low noise, high efficiency, long service life, minimal maintenance
- Common Uses: Drones, servo mechanisms, medical devices, compact fans, electric scooters
Chapter 5|Motor Control and Drive Techniques
Modern motors aren’t just about spinning—they’re about spinning with precision, responsiveness, and efficiency.
🔸 PWM Control (Pulse Width Modulation)
By adjusting the width of current pulses, the motor’s average voltage and power can be precisely controlled. This is the most common method for smooth speed regulation.
🔸 Speed vs Torque Control
- Speed Control: Keeps the motor rotating at a set rate (e.g., a fan running at 1200 RPM)
- Torque Control: Maintains consistent output force—useful in electric vehicles when climbing or accelerating
🔸 Motor Drivers / ESCs
Whether for DC or BLDC motors, a motor driver (or ESC for BLDCs) is needed to control operation.
- Functions: Distribute power, handle switching (commutation), protect against overloads
🔸 Sensor Feedback: Hall Sensors and Encoders
For accurate positioning and speed feedback, motors may include:
- Hall Sensors: Detect magnetic field changes to determine rotor position
- Rotary Encoders: Provide high-resolution feedback on position and speed—essential for servo control systems
Chapter 6|Electric Motors in Everyday Life and Industry
Electric motors are embedded in almost every modern system. Here are four major categories of application:
✅ Home Appliances
- Washing machines: Control drum spin and drainage
- Air conditioners: Use induction motors for compressors and fans
- Vacuum cleaners, desk fans, electric toothbrushes: Use DC or BLDC motors for compact and smooth motion
✅ Industrial Equipment
- CNC machines: Use servo motors for precision head positioning
- Conveyor systems & robotic arms: Combine induction motors with encoders for automation
- Pumps and blowers: Primarily driven by three-phase AC motors
✅ Transportation
- Electric vehicles (EVs): Use BLDC or induction motors as primary drive units
- E-bikes and scooters: Typically equipped with compact brushless DC motors
- Trains and metros: Rely on three-phase synchronous or induction motors for propulsion
✅ Medical Devices
- Adjustable hospital beds, electric wheelchairs: Focus on safety and consistent torque
- Surgical robotic arms: Require ultra-precise servo motor control
- Ventilators and suction devices: Use small DC or brushless motors to drive internal pumps
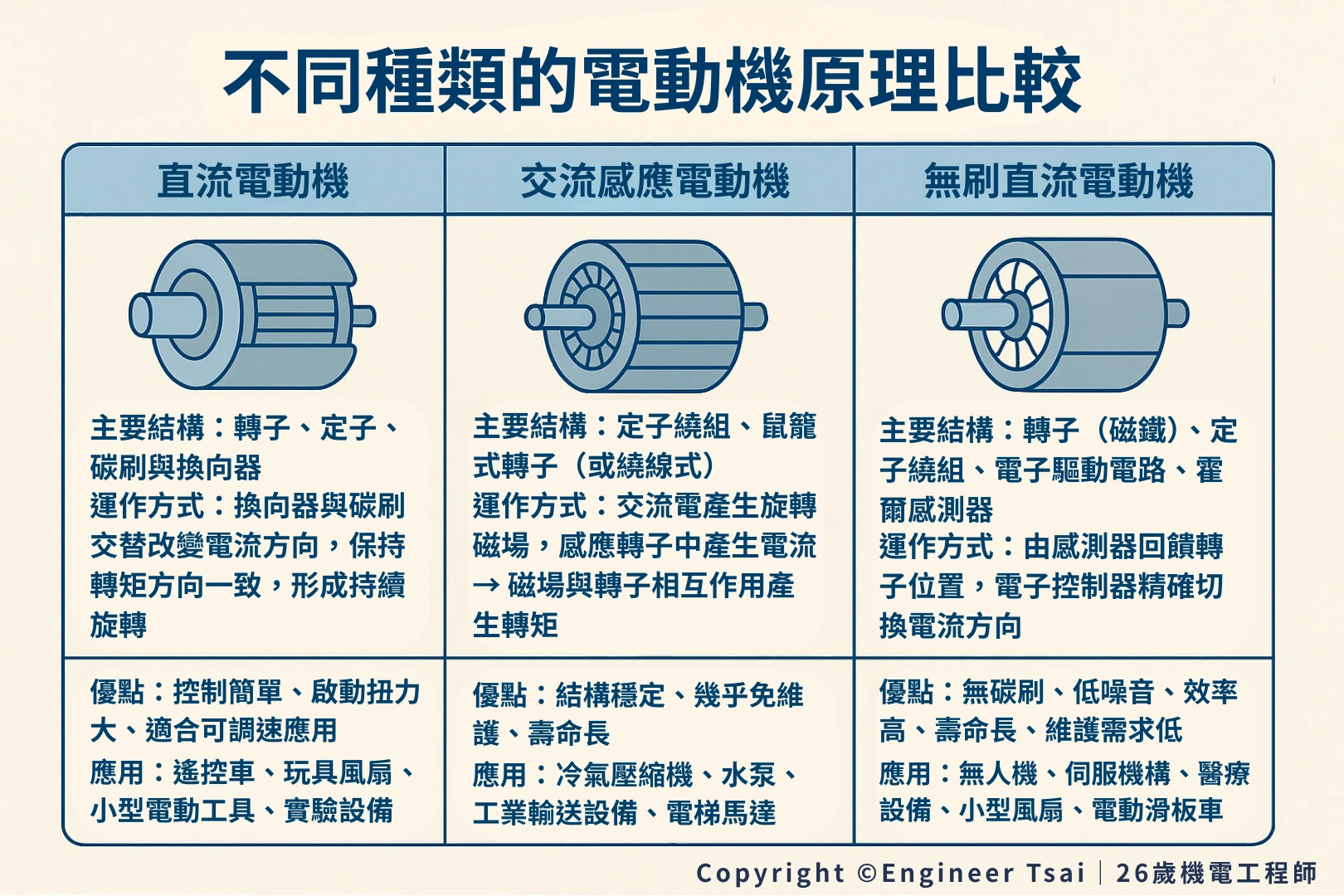
Chapter 7|The Evolution of Electric Motors: From Theory to Technology
The invention and evolution of electric motors is a remarkable reflection of humanity’s growing mastery over electromagnetism. From 19th-century scientific breakthroughs to modern smart applications, each step has profoundly shaped both our daily lives and industrial progress.
🔹 Maxwell’s Electromagnetic Foundations
In the 19th century, James Clerk Maxwell, a British physicist, developed the comprehensive theory of the electromagnetic field. His equations unified electricity and magnetism, providing the mathematical backbone for how electric motors operate.
🔹 Faraday’s Experiments and the Reverse Principle
In 1831, Michael Faraday discovered electromagnetic induction—when a conductor cuts through a magnetic field, it generates current. While this phenomenon gave rise to generators, it also laid the groundwork for electric motors, which operate on the reverse principle.
🔹 Edison vs. Tesla: The Battle of DC and AC
- Thomas Edison promoted the use of direct current (DC) systems and brushed DC motors, suitable for early urban power grids and industrial machines.
- Nikola Tesla, on the other hand, championed alternating current (AC) systems and developed induction motors. Due to better efficiency and long-distance transmission, AC ultimately became the global standard.
🔹 Modern Developments: Brushless, Miniature, and Smart
With advances in materials, control electronics, and magnetic components, motors have evolved along these lines:
- Brushless (BLDC): Higher efficiency, lower maintenance
- Miniaturization: Used in wearables, medical tools, robotics
- Smart Control: Equipped with sensors and algorithms for precision torque and speed control
Chapter 8|Common Motor Issues and Basic Troubleshooting
Electric motors are known for their simplicity and durability, but they’re not immune to wear and faults. Here are some common problems and basic solutions:
⚠️ Unusual Noise During Operation
- Possible Causes: Worn bearings, misaligned shafts, loose components
- Recommended Fix: Check and lubricate bearings, tighten loose parts, replace worn components
⚠️ Failure to Start
- Possible Causes:
- DC motors: Worn brushes, oxidized commutator
- AC motors: Faulty start capacitor, burned coils
- General issues: Motor overload, damaged controller
- Recommended Fixes:
- Measure input voltage to verify power supply
- Test and replace capacitors (especially in single-phase AC motors)
- Replace brushes or clean the commutator surface
⚠️ Overheating
- Possible Causes: Excessive current, blocked ventilation, prolonged overload
- Recommended Fixes: Clean vents and fans, ensure load is within rated limits, add heat sinks or thermal protection
🧰 Maintenance Tips
- Regularly clean housing and intake vents
- Inspect brushes for wear every few months
- For long-unused motors, start with low-speed test runs
- Stop immediately if there’s vibration or abnormal noise
Chapter 9|Try It Yourself: A Simple DIY Motor Experiment
Want to see how electricity becomes motion firsthand? Try this easy motor experiment at home—no fancy tools required!
📦 Materials Needed:
- 1 × AA battery (1.5V)
- A short length of thin copper wire (stripped)
- 1 × small neodymium magnet
- 2 × paper clips or metal holders (to serve as supports and conductors)
🛠 Steps to Build:
- Bend the copper wire into a circular coil, leaving both ends straight to act as axle shafts
- Attach the magnet to the bottom of the battery
- Use paper clips to hold the battery upright and make contact with both terminals
- Place the coil between the supports, ensuring the ends can spin freely and conduct electricity
- Once current flows, the coil will begin to spin!
🔍 Observation and Explanation:
- This is a basic demonstration of motor principles
- Rotation occurs due to Lorentz force, as current flows through the coil in a magnetic field
- As the coil turns and loses contact, the rotation stops—you can maintain it by creating a simple commutator
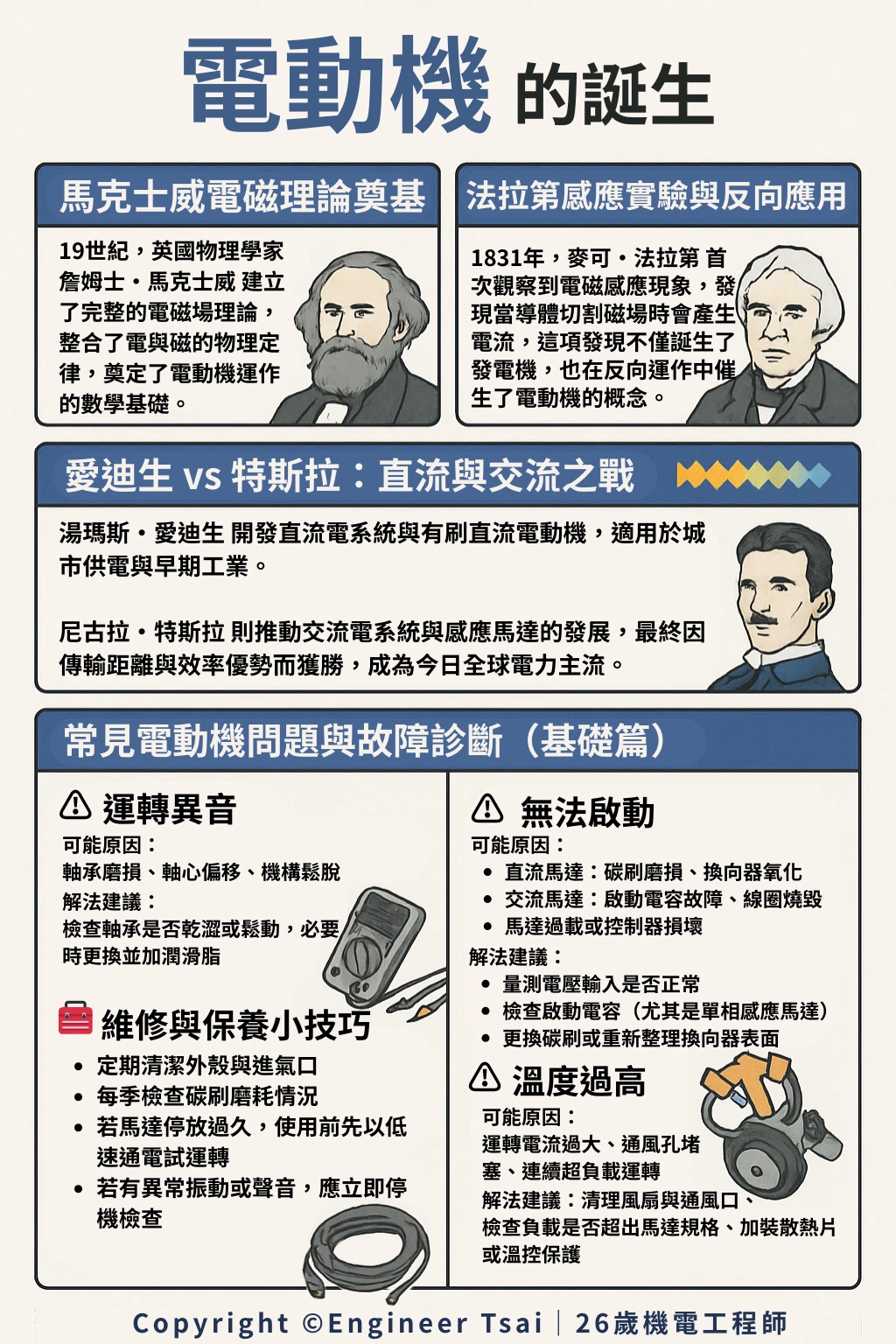
Conclusion & Further Reading
Electric motors are the unsung heroes behind the transformation of electricity into motion. From home appliances and transportation to industrial automation, motors are at the core of countless systems. Understanding how they work not only helps us design more efficient machines and troubleshoot problems more effectively, but also deepens our appreciation of the fascinating link between electricity and movement.
📌 Recommended Reading:
🔹 [Faraday’s Law of Electromagnetic Induction: Simple Guide with Real-World Uses]
Discover the fundamental physics behind motor operation—how magnetic fields and electric current interact to create motion.
🔹 [How to Generate Electricity Using an AC Generator]
Understand the reverse application of motor principles—motors and generators are two sides of the same coin.
🔹 [How Do DC Generators Work? The Secret to Stable Current Output] (Coming Soon)
Motors rely on stable power sources, and DC generators were once the backbone of early electromechanical systems.
🔹 [How Do Electric Vehicle Motors Work? 3 Common Types Explained] (Coming Soon)
Curious about high-efficiency motor technology? Learn how BLDC, induction, and PMSM motors power modern EVs.